Plastic Injection Molding
On-Site Completion
We’ve got you covered
DRS utilizes an advanced mold making process to facilitate the needs of our customers. Our highly skilled team and precision equipment combine to provide you with simple or complex parts that meet your quality requirements, not ours! From 100 parts up to 10,000 parts at a time, we will build the right tool for your product. DRS can provide you with a vast array of injection molding products whether your part has undercuts, molded inserts, tight tolerances, or over molding. There is no part we won’t review, and we are not afraid of taking on a challenge.
Services Include:
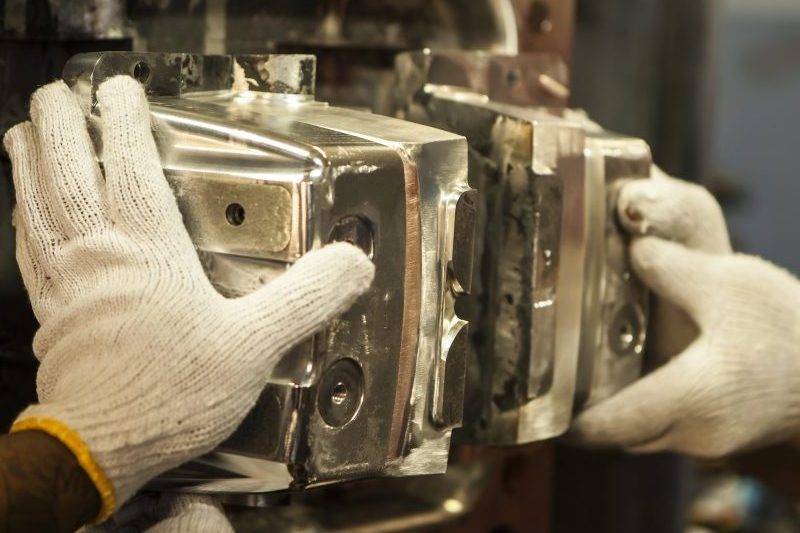
Material Selection: This is one of the most important decisions when starting a new project and figuring out what type of resin is going to fulfill the design and functional requirements of your product. Below are some common materials that are used in the injection molding process. When in doubt, always contact a resin supplier to find the best possible match for your product. DRS has molded hundreds of different materials, however that does not mean we know the best material for your product. We are here to guide you and our DFM process can help determine if your design is built for your selected material.
Strong heat resistance.
High tensile strength.
Scratch resistance.
Good Weatherability.
Excellent Rigidity.
Abrasion Resistance.
Creep Resistance and Solvent Resistance.
Low Coefficient of Friction.
High Resolution Clear Resin.
Non-Yellowing Color.
Good Weatherability.
Strong Heat Resistance.
High Tensile Strength.
Scratch Resistance.
Dimensional Stability.
Optical Clarity.
High Heat Resistance.
UV Resistance.
High Impact Resistance.
Chemical Resistance
Elasticity and Toughness.
Fatigue Resistance.
Good Insulation.
Transmissivity.
Water Resistant
Elasticity and Good Toughness.
Self Lubricating.
Lightweight and Strong.
Good Moldability.
High Strength.
Very Good Dimensional Stability.
High Heat Resistance.
Chemical Resistance.
Good Moldability.
High Strength.
Very Good Dimensional Stability.
High Heat Resistance.
Chemical Resistance.
Good Rigidity.
General Purpose Material.
Low Cost Material.
High Tensile and Impact.
Strength Flexibility and Elasticity.
Thermal and Chemical Resistance.
Higher Tensile and Impact.
Better Dimensional Stability.
High Heat Resistance.
Strength Flexibility and Elasticity.
Thermal and Chemical Resistance.
Shock Absorption.
Great Flexibility.
Simplified Processing.
Soft Touch Texture.
Great UV Resistance.
Good Flexibility.
Good Impact Resistance.
Great Wear Resistance.
High Abrasion Resistance.
Lowers Vibration.
High Impact Resistance.
Great Mechanical Resistance.
Good for Overmolding.
Excellent Flame and Heat Resistance.
Resistance to Stress and Cracking.
Great Rigidity at High Temps.
Great Dimensional Stability.
Good electrical Properties.
Improved Fatigue Strength and Creep Resistance.
Great Weatherability.
Excellent Abrasion Resistance.