Tooling
Low Cost, Fast Delivery, Short Cycle Time
The most critical element to an injection molded part is the tooling. At DRS, we utilize a complete tool making system that allows us to customize your tool depending on the material and function of your part. Why pay more money for a tool if it is not needed? We evaluate your project and build a tool that fits your needs. DRS has been building quality tools that last for more than 35 years. DRS builds tools for prototyping, low volume production, and higher volume production. Your product has a need, we have a tooling solution. Our rapid cut tooling solutions focus on:
Because we fully 3D model and detail every mold component, customer driven part design changes can be incorporated quickly, while protecting your development budget.
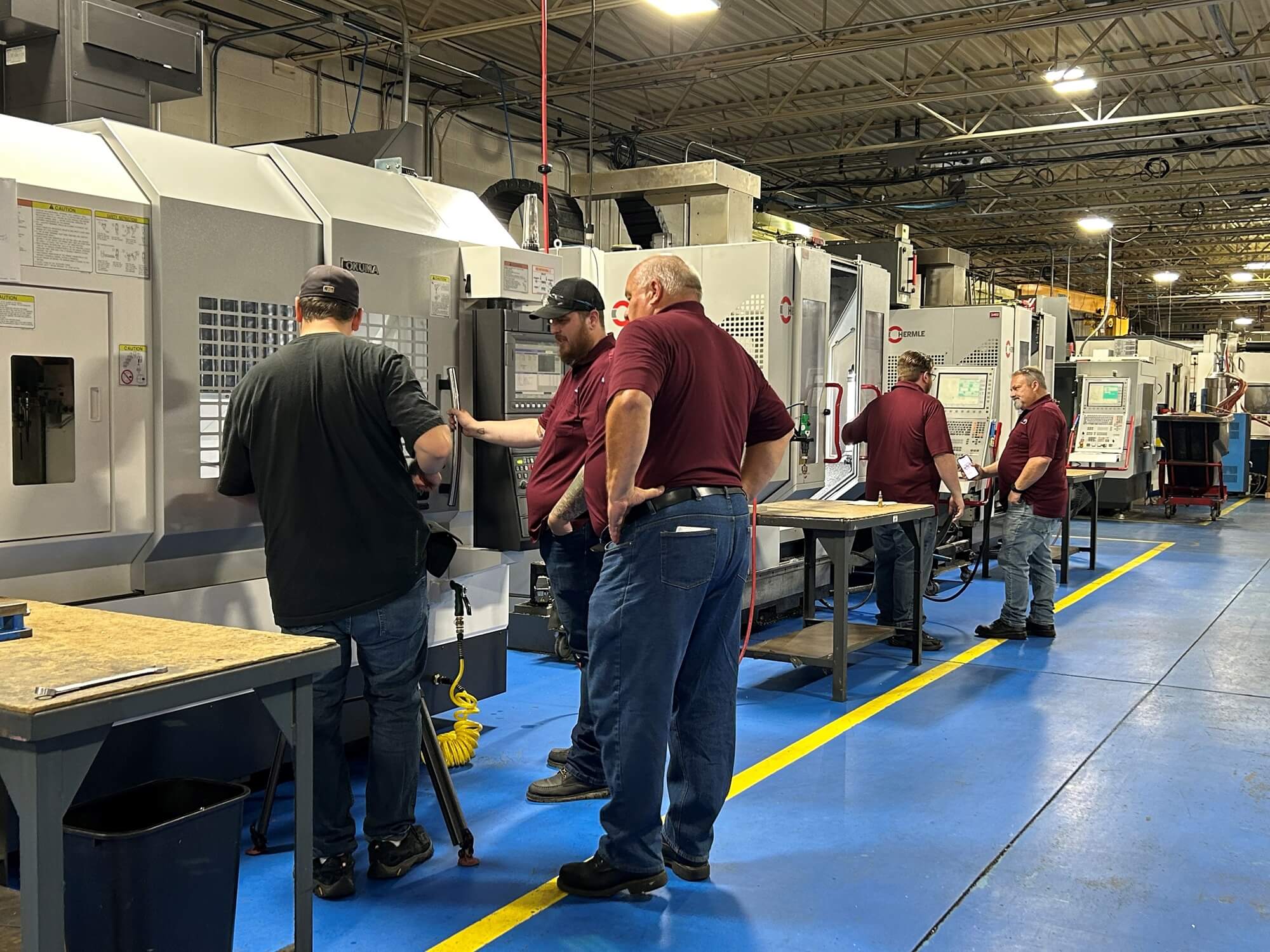
WHY USE ALUMINUM TOOLING???
QC10 Aluminum
QC-10 is among the first aluminum alloys specifically designed for a variety of mold making applications. QC-10 combines the high thermal conductivity of aluminum with higher hardness and strength, more uniform properties through thickness, and greater corrosion resistance than previous aluminum alloys. Available in thicknesses from 1 inch to 32 inches, QC-10 possesses extremely low quench sensitivity which assures mold makers of consistent machining through the entire thickness of the plate. QC-10 is full wrought, tempered, and stress relieved prior to delivery.
QC-10 has been successfully substituted for P-20 in production injection molds making in excess of one million cycles. The tight grain structure allows for outstanding machinability with small chips, outstanding surface finish, very few burrs, and very fast CNC feeds and speeds. QC-10 can also be polished to a very fine finish (SPI A2). Many molds have been constructed of aluminum employing slides and lifters.
Benefits
- Lower part cost through reduced cycle time (25% – 40% typical reduction).
- Higher thermal conductivity permits flexibility in water line placement and simplifies cooling system design.
- Up to 10 times faster metal removal rates than P-20.
- Shorter mold build lead times.
- Reduced wear and down time on molding equipment due to the lower weight of QC-10 vs. P-20.
- Better corrosion resistance than other high strength aluminum alloys.
- Eight times higher thermal diffusivity than steel. Material with higher thermal diffusivity rapidly adjusts its temperature to that of its surroundings.
- More uniform temperature distribution throughout the mold and the elimination of hot spots.
- QC-10 is delivered fully heat treated and stress relieved. No further heat treat or stress relief is necessary
- All data you see provided by Thyssen Krupp; Copper and Brass.