Prototyping
Injection Molded Parts
For when you need it Quickly or at a Lower Cost
Whether you are looking to test form, fit, and function, run a beta test, or validate potential cosmetics of a part; DRS can provide you with fast and affordable prototype injection molded parts to assist the early stages of development on your project. If printed parts or CNC machined parts will not cut it, get production level parts from a prototype tool that can provide anywhere from 5-500 parts and get them in a matter of weeks, not months. Our custom tooling approach allows for a cost-effective way to get prototype parts fast. See how DRS can help make your program come to life!
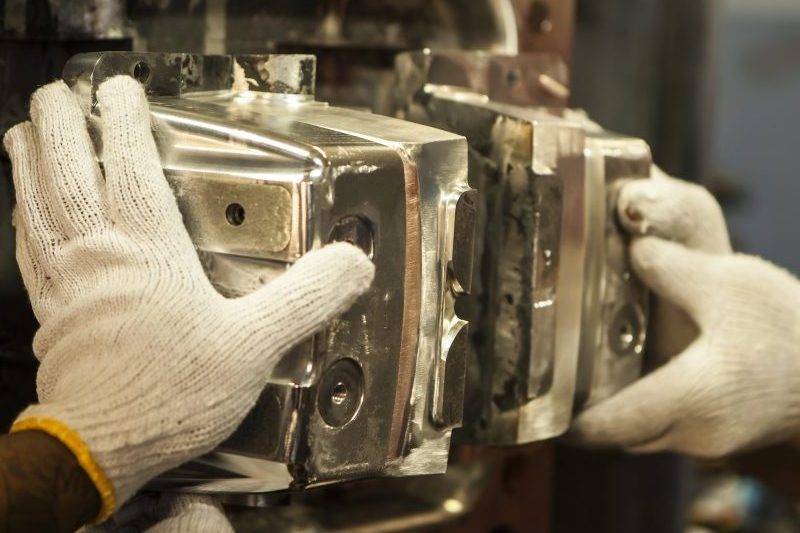
Printed parts vs molded parts: what is the big difference?
So how do you choose the right method? To break it down, you simply need to ask yourself the question, what is the function of my prototype? Do you visually want to see the part, so you can make sure it feels correctly in your hand, maybe you want to assemble something together or you have a mating part you need to check the fit? You may want to see if it is even functional altogether. For simple purposes such as these, you could consider the printing process, where a printed plastic material creates and forms your part. The layering process does not create a molded part with the same properties and in some ways is quite limited.
Another method is an injection molded part created with a low-cost tooling method. DRS can build a tool that specifically fits your need associated with testing that part. Most people creating a part that is an integrated feature on a larger assembly, want to make sure their part will perform to the standard needed. Therefore, they want a fully molded part that will showcase the correct properties in testing. This also allows them to see exactly how the product will perform in a production setting as this will mimic that level of manufacturing. Many will refer to this as soft tooling or quick turn injection mold tooling. Either way you could mold, test, and make design changes in a cost-effective way to fully prepare for the production process. Overall, a great method for prototyping your next project to fully prepare for the production process.